Detailed Explanation of Outdoor Wall Lamp Processing Technology
2025-04-22
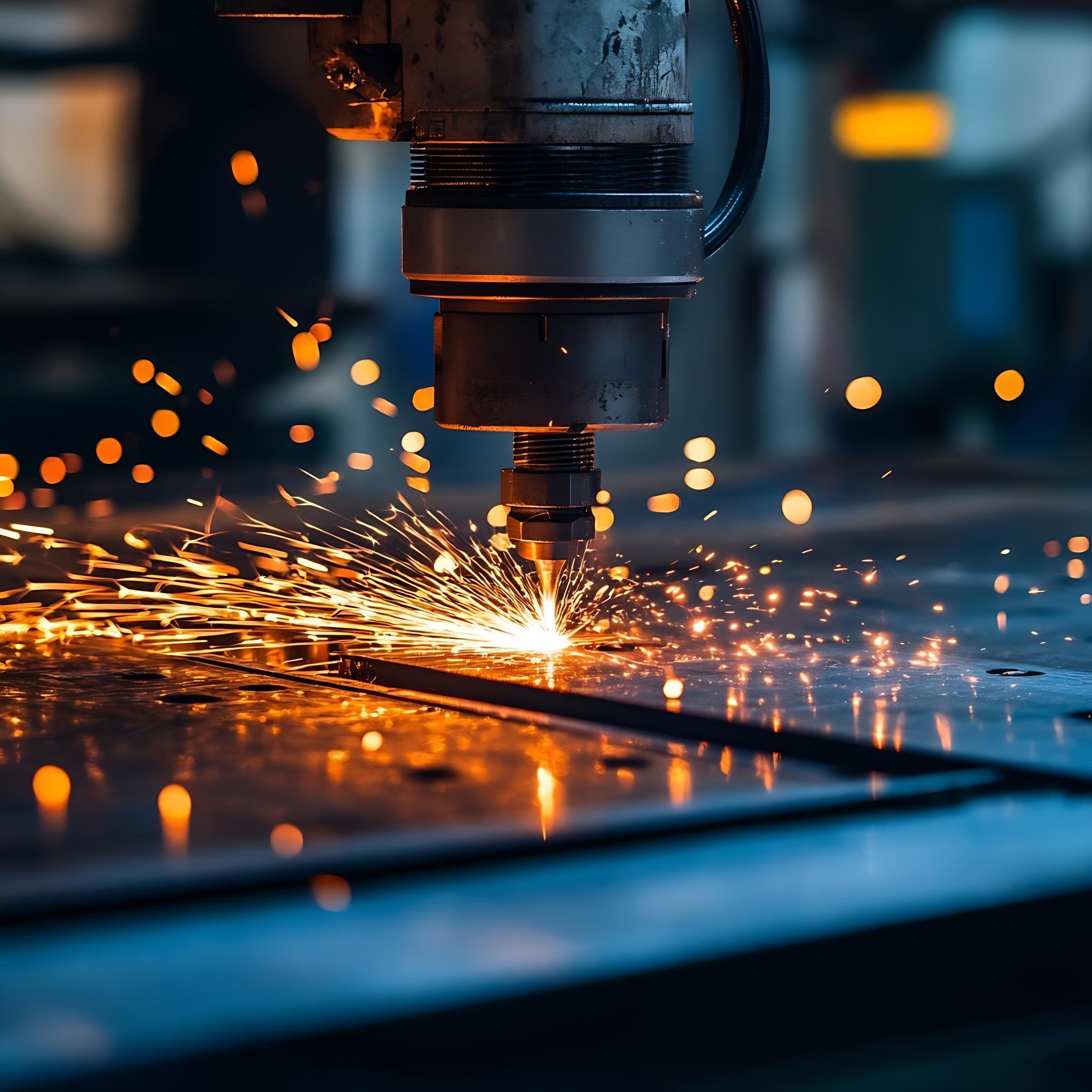
Main processing technology
(a) Metal processing
Die casting (applicable to aluminum alloys and zinc alloys) :
Molten metal is injected into the mold through high pressure to form complex structures such as the lamp body and the base.
Advantages: High precision, high production efficiency, suitable for mass production.
Stamping forming (applicable to steel plates and stainless steel) :
Metal sheets are cut and bent using punch presses and molds to make lamp bodies or brackets.
Advantages: Low cost, suitable for standardized production.
CNC precision machining (applicable to high-end custom lamps) :
High-precision structures are achieved by milling and drilling metals through CNC machine tools.
Advantages: It can process complex shapes, but the cost is relatively high.
(b) Surface treatment (anti-rust, aesthetic)
Spraying (plastic spraying/painting) :
The electrostatic spraying technology is adopted to make the powder coating adhere evenly, and then after high-temperature curing, a wear-resistant and corrosion-resistant protective layer is formed.
Common colors: black, white, bronze, champagne gold, etc.
Electroplating (applicable to stainless steel and copper) :
Chromium, nickel or copper plating is carried out on the surface through electrolytic processes to enhance corrosion resistance and gloss.
The process of "copper wire drawing + electroplating for rust prevention" can enhance the retro texture.
Anodizing (applicable to aluminum alloys) :
An oxide film is formed on the surface of aluminum through electrolysis to enhance its hardness and weather resistance, and it can also be colored (such as black and gold).
(c) Lampshade processing
Glass lampshade
It is made of tempered glass or frosted glass through processes such as hot bending, cutting and printing.
Advantages: Good light transmission and strong sense of luxury.
PC/ Acrylic lampshade
It can be made into various shapes through injection molding, and an anti-UV coating is added to prevent yellowing.
Advantages: Lightweight, impact-resistant, suitable for modern-style lamps.
(d) Assembly and sealing
Waterproof structure design
Silicone rubber sealing rings, waterproof glue or ultrasonic welding process are adopted to ensure that the lamp body reaches IP65 or above protection level.
Installation of electrical components
Built-in drive power supply (such as LED constant current driver), terminal blocks, and aging tests are conducted to ensure stability.
Previous: